‘Bite the Bullet’ and Buy New Boots: 3 Greenhouse Produce Lessons from Abby Lange
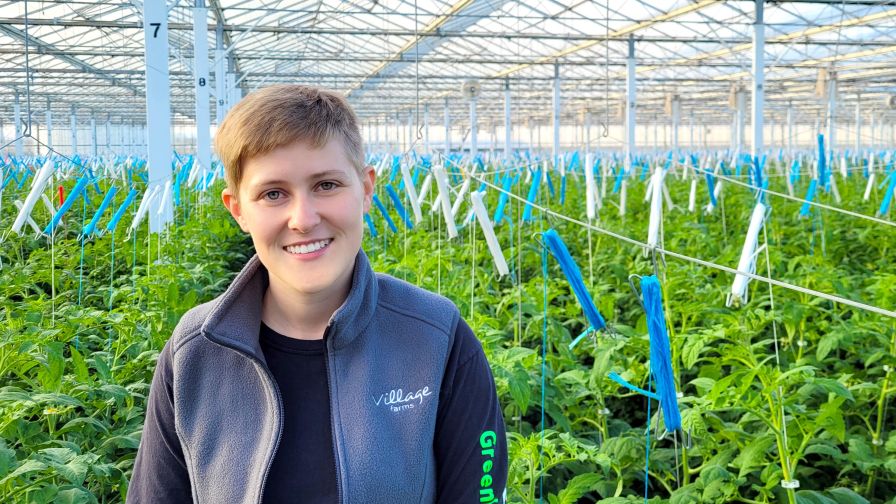
Abby Lange of Village Farms.
In the more than eight years since Abby Lange started working with Village Farms Fresh as an intern, she proved herself time after time, eventually advancing into the facility manager role at the North American business’s Marfa I greenhouse in Texas’ Chihuahuan Desert.
“I grow on 20 acres, and this is the small facility of the company,” she says. “It’s the baby facility of the company.”
Jest aside, as the facility that Lange manages is gargantuan, so are the lessons that come with ensuring that Village Farms meets on-the-vine tomato production goals, potential returns on investments are being properly calculated and employees are productive and engaged.
Below are just a few nuggets of wisdom that Lange has gleaned so far.
1. Be ready to adapt.
The produce industry faces challenges such as natural resource limitations and supply chain disruptions, but Lange says she is excited about growers’ resiliency and ability to tackle them.
“There are a lot of areas already undergoing a lot of water scarcity, big tomato-growing areas, California, Morocco—and we grow in a desert,” she says. “We get it, that this is a precious natural resource. And we, I think, have such an advantage when it comes to being able to have high yields per acre while actually reducing water usage by a crazy amount.”
Lange also mentions how the industry has needed to reduce its reliance on fertilizer since the war in Ukraine has restricted supply. “I think that we’re already really far ahead of the game in terms of those things,” she says. “But I know we can push it further, and we’ll be there for the long haul.”
As Lange stares down these and other large obstacles, a certain philosophy is at play.
“We live in a world that places a lot of demands on you, and we work in an industry that’s constantly in flux,” she says. “But stressing out is never the answer, and it’s never going to help you find the answer you need in a situation. So, it’s better to just keep a cool head and focus and use that energy that you would be spending worrying on anything else.”
2. Research possible returns on investments.
When evaluating whether to implement new technologies, Lange says it’s important to understand how those technologies work.
“And if you don’t understand how they work and if it’s totally out of your league, find somebody who’s in that branch of research or of industry,” she says.
Lange also shares a version of the adage that sometimes you’ve got to spend money to make money—and offers up an anecdote.
“I had a conversation one time with a coworker about shoes because anyone who works in greenhouses will know your shoes are put through the ringer in this industry,” she says.
The employee said he was spending $30 on shoes, but they only lasted him two months. Lange says her $120 boots last her two years.
“Sometimes it is better to just bite the bullet and invest in something that’s going to work for you,” she says. “And knowing where that difference will be made and where extra dollars invested will save you more later on is key, for sure.”
3. Make recruiting and training processes versatile.
When recruiting for positions, Lange says she likes promoting from within because it’s an easy transition for the in-house job candidate and their colleagues.
However, welcoming newcomers to an operation with or without industry experience can bring fresh ideas and perspectives, she says.
In that context, Lange says: “For me, that’s the first thing, is just not being so quick to say, ‘Well, this person doesn’t fit exactly in this category, doesn’t have this neat, little bundle of experience and education that perfectly aligns with what we’re doing.’ But if you have somebody who really has drive to learn and to improve things, then that person’s still worth their weight in gold.”
Employee cross-training is also important, she says, because another position might become available or someone might need to pick up the responsibilities of another team member who is unable to work. Also, team members who learn new processes display ambition, which is a positive quality among candidates for open positions.
“So, we want to make sure that they’re not in over their heads or lost when that comes to pass,” Lange says.
Listen to this conversation with Abby Lange on Greenhouse Grower’s Grower to Grower Podcast.