Grow Up: Bringing Vertical Farming Systems To Greenhouses
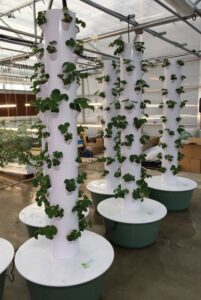
Tower garden with hydroponic strawberries
Vertical farming systems are a well-established technology in indoor farms. By integrating lighting fixtures into vertical cultivation racks and adapting climate control systems to the increased heat and humidity loads, indoor farmers can maximize their facility production by using its cubic footage instead of solely relying on their building’s square footage.
Greenhouses, however, seldom use these vertical farming systems and techniques. And there are good reasons for this. Vertical farming systems can limit the amount of natural light reaching crops placed on lower levels, forcing growers to rely more heavily on supplemental lighting, which in turn increases production costs. With greenhouse crop margins as thin as they are (outside of cash crops like cannabis), an over-reliance on supplemental lighting can be the difference between a healthy business and an unviable structure.
That said, there are ways for greenhouse producers to integrate vertical farming systems into their cultivation processes, even if they require more forethought and planning. Here, we explore how you can integrate vertical farming practices and technologies into your greenhouse operation to increase your resource efficiency and facility efficacy.
Move propagation into the headhouse with vertical racks
Propagating cloned cuttings or sprouting seeds requires a completely different environment to maturing and mature plants that can be much more resource-intensive to maintain. For example, temperature and humidity targets may be higher, forcing greenhouse operators to modify a bay or zone within their range, significantly reducing production capacity.
Assuming that propagation happens on single-tier trays and that 10% of the 100,000 square feet of canopy space is allocated to propagation, that leaves 90,000 square feet for mature plant cultivation.
Using vertical racks, growers can condense those activities to free up more canopy space for mature plants. Based on the assumption that the vertical racks measure 8 feet by 4 feet and have six levels, propagation activities can be condensed to approximately 1,667 square feet, leaving 98,333 square feet of canopy space. (These rough estimates do not account for space needed for aisles and cultivation equipment.)
However, there are other practical reasons why vertical racking systems may not be a suitable greenhouse retrofit. Standard greenhouses with mechanical cooling aren’t designed for a vertically uniform temperature. The temperature climbs rapidly in the upper layer, beginning just a few feet above the heights of the intake vents, evaporative cooling pads, and exhaust fans. This might be mitigated by fog cooling, but those systems require a clearance of 3-4 feet from the nozzles, reducing the available height. The placement of the racks would greatly reduce the airflow needed for ventilation and air circulation.
Pest control is another challenge for this retrofit, as standard greenhouses typically have much greater infestation issues than indoor farms that require routine sprays, which would be more difficult to apply uniformly in a vertical rack.
Bringing the propagation into a dedicated room with vertical racking inside the headhouse or another indoor structure may be a creative solution that would optimize space efficiency and crop production. While this move would require additional HVAC capacity, these small-scale indoor environments can more easily maintain the environmental specifications for seed and/or clone propagation, increasing root production and plant vigor. Hybrid CEA and greenhouse food crop producer Local Bounti is leveraging its proprietary Stack and Flow technology in this exact way.
Research has shown that great improvements in propagation can be achieved by modifying the temperature, humidity, and lighting according to the four stages of seedling production: seeding to initial root emergence (stage 1); initial root to flat cotyledons (stage 2); flat cotyledons to first true leaf (stage 3); first true leaf to transplantable size (stage 4).
A similar sequence has been determined for clonal rooting. In addition to improved seedling or cutting vigor, providing high light during the propagation stage has been shown to improve yield at harvest on some species, including basil, dill, and sage. These optimized propagation environments are more likely to be achieved in a well-designed indoor environment, with the added benefit of isolation from the greenhouse, filtered airflow, and fewer pests.
Given the use of vertical racking for both seeding and tissue-culture production at research facilities, might isolated, optimized indoor propagation facilities be well-suited for crops that are virus-indexed, such as strawberries and tomatoes?
Greenhouses could use such facilities for propagating plants for the small, specialty markets such as uncommon culinary herbs, edible flowers, and carnivorous plants. Regardless of how they would be used, greenhouses would become more efficient by having fewer environments to maintain, more space for production, and cleaner, more vigorous propagation material.
(It is important to note when using lighting fixtures within the vertical racks that too much light can stress certain plants, bleach leaves, and reduce root formation, as noted in RII’s Lighting Best Practices Guide. Lower-intensity fixtures, or those with tunable intensities, are recommended when propagating in vertical racks.)
Considerations when integrating vertical farming in post-propagation production
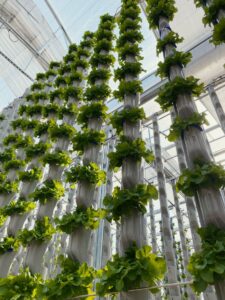
Eden Green Technology’s vertical farming system in their greenhouse
While not particularly common yet, some commercial greenhouses (especially hybrid structures like this South Korean operation, or this concept from KG Systems, or even Local Bounti and Eden Green in the U.S.) are utilizing vertical farming systems effectively in their cultivation areas.
A couple of factors have made greenhouse vertical farming a possibility. The first is that North American greenhouses, especially, have become taller and wider, explains Anders Peterson, Director of Horticulture at RII-member organization Pipp Horticulture. “The old cut flower greenhouses here in the central valley in California, they used to have 10-foot gutter heights, … and now we’re looking at 20-, 24-foot gutter heights.”
These taller and wider designs increase the total air volume within the structure, which provides a buffer against rapid temperature and humidity fluctuations. “By having a taller gutter height, … there’s more headspace for heat to rise in the house and to be vented out of the roof depending if it’s a passive or active type of greenhouse,” Peterson adds.
The second evolution in greenhouse design that makes vertical farming a possibility is the popularization of light-diffusing technologies such as curtains or glazing, which spreads photons out inside the structure instead of letting them freely pass through the glass. “So even if you do have support columns or gutters in the way, this diffused glazing [or curtain] perceptibly minimizes that because it scatters the light photons all around the house so that you don’t get the shadowing effect as much,” he details. Growers will need to be mindful of the impact light diffusion will have on intensity and spectral uniformity. Lower shelves may require more LED fixtures to achieve the same PPFD and spectrum that higher racks receive via sunlight.
Without both of these developments, bringing vertical farming systems into a greenhouse becomes an exercise in building an indoor farm, which, again, works against a greenhouse’s main benefit–free sunlight.
Regardless of the type of vertical farming method used (horizontal planes, A-frames, vertical tubes, fully automated systems that cycle racks toward sunlight, and other bleeding-edge designs being researched and trialed globally), the impacts on the cultivation environment are similar to those seen in tiered indoor farms, namely increased heat and moisture loads. While taller greenhouses have a larger buffer zone, facility operators will still need to be mindful of mitigating microclimates within the vertical tiers.
“Microclimates are one of the top things people bring up–mitigating microclimates, [having] even airflow, [having] even VPD throughout the canopy. Well, now that becomes an even greater challenge in a greenhouse because you have less of an R-value, less insulation in the structure, and these swings are greater. The deviations in your microclimates are hotter and more humid, or colder and drier,” Peterson notes.
This may force greenhouse growers to use mechanical cooling systems rather than relying on passive climate control techniques. Depending on the crop, facility location, and market demand, this may or may not make the facility viable. Operators must take a close look at their profit and loss statements (P&Ls) when determining a jump to vertical farming systems.
Researchers wanted (and needed)
Bringing vertical farming systems into greenhouse environments is an interesting proposition, Peterson says, and one that is still in its early stages of research and development. More data is needed to determine in which scenarios integrating vertical farming makes sense for greenhouse operators.
“There are challenges to growing vertical in a greenhouse today,” Peterson notes. “I think there’s still a lot to be learned and a lot of this puzzle to be solved. I’m not saying it’s impossible, but there needs to be more innovation in this area and more research to study some of the design aspects required to make this crop production model viable. People need to take risks. They need to try this thing and they need to compare it to the next best alternative and see if it’s really better.”
With more data, more partnerships between governments, academia, and private enterprises, and more time, greenhouse operators have the opportunity to take the next leap in efficient production. To those willing to take those risks, know that it won’t be perfect on the first attempt, but it is just as important to know what is not operable as it is to know what works.